انتخاب درمان سطحی مشکلی است که هر طراح با آن مواجه است.انواع مختلفی از گزینه های تصفیه سطح موجود است و یک طراح سطح بالا نه تنها باید صرفه جویی و کاربردی بودن طراحی را در نظر بگیرد، بلکه باید به فرآیند مونتاژ و حتی الزامات محیطی نیز توجه کند.در زیر به معرفی مختصری از برخی از پوششهای متداول استفاده شده برای اتصال دهندهها بر اساس اصول فوق، برای مراجعه متخصصان بست میپردازیم.
1. الکتروگالوانیزه کردن
روی رایج ترین پوشش مورد استفاده برای اتصال دهنده های تجاری است.قیمت نسبتا ارزان است و ظاهر خوب است.رنگ های رایج شامل مشکی و سبز نظامی است.با این حال، عملکرد ضد خوردگی آن متوسط است و عملکرد ضد خوردگی آن در بین لایه های روکش روی (روکش) کمترین است.به طور کلی، آزمایش پاشش نمک خنثی فولاد گالوانیزه در عرض 72 ساعت انجام می شود و از مواد آب بندی مخصوص نیز استفاده می شود تا اطمینان حاصل شود که آزمایش پاشش نمک خنثی بیش از 200 ساعت طول می کشد.با این حال، قیمت گران است، که 5-8 برابر فولاد گالوانیزه معمولی است.
فرآیند الکتروگالوانیزه مستعد شکنندگی هیدروژن است، بنابراین پیچ های بالاتر از درجه 10.9 معمولاً با گالوانیزه درمان نمی شوند.اگرچه بعد از آبکاری می توان هیدروژن را با استفاده از کوره حذف کرد، فیلم غیرفعال در دمای بالای 60 درجه سانتیگراد آسیب می بیند، بنابراین حذف هیدروژن باید پس از آبکاری الکتریکی و قبل از غیرفعال سازی انجام شود.این عملکرد ضعیف و هزینه های پردازش بالایی دارد.در واقع، کارخانه های تولید عمومی به طور فعال هیدروژن را حذف نمی کنند، مگر اینکه توسط مشتریان خاص اجباری شود.
قوام بین گشتاور و نیروی پیش سفت بست های گالوانیزه ضعیف و ناپایدار است و معمولاً برای اتصال قطعات مهم استفاده نمی شود.به منظور بهبود قوام پیش بار گشتاور، می توان از روش پوشش مواد روان کننده پس از آبکاری نیز برای بهبود و افزایش قوام پیش بار گشتاور استفاده کرد.
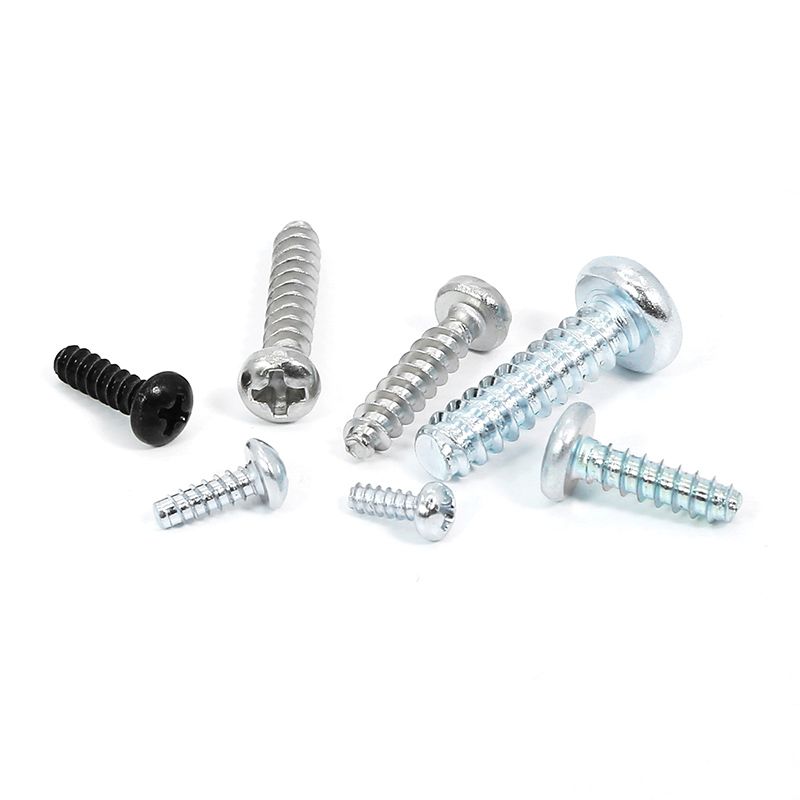
2. فسفاته کردن
یک اصل اساسی این است که فسفاته کردن نسبتاً ارزان تر از گالوانیزه است، اما مقاومت در برابر خوردگی آن بدتر از گالوانیزه است.پس از فسفاته کردن، روغن باید اعمال شود و مقاومت در برابر خوردگی آن ارتباط نزدیکی با عملکرد روغن اعمال شده دارد.به عنوان مثال، پس از فسفاته کردن، استفاده از یک روغن ضد زنگ عمومی و انجام آزمایش پاشش نمک خنثی تنها به مدت 10-20 ساعت.استفاده از روغن ضد زنگ با درجه بالا می تواند 72 تا 96 ساعت طول بکشد.اما قیمت آن 2-3 برابر روغن فسفاته عمومی است.
دو نوع متداول فسفاته کردن برای اتصال دهنده ها وجود دارد، فسفاته کردن بر پایه روی و فسفاته کردن بر پایه منگنز.فسفاته بر پایه روی عملکرد روانکاری بهتری نسبت به فسفاته کردن بر پایه منگنز دارد و فسفاته سازی بر پایه منگنز نسبت به آبکاری روی مقاومت به خوردگی و مقاومت در برابر سایش بهتری دارد.می توان از آن در دماهای بین 225 تا 400 درجه فارنهایت (107-204 ℃) استفاده کرد.به خصوص برای اتصال برخی از اجزای مهم.مانند پیچ و مهره شاتون موتور، سرسیلندر، یاتاقان اصلی، پیچ فلایویل، پیچ و مهره چرخ و غیره.
پیچ و مهره های با استحکام بالا از فسفاته کردن استفاده می کنند که می تواند از مشکلات شکنندگی هیدروژن نیز جلوگیری کند.بنابراین، پیچ و مهره های بالاتر از درجه 10.9 در زمینه صنعتی به طور کلی از عملیات سطح فسفاته استفاده می کنند.
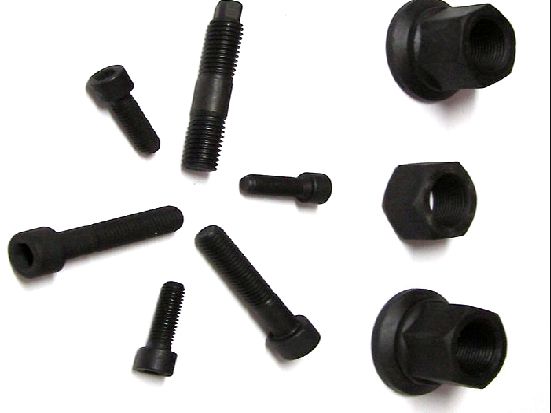
3. اکسیداسیون (سیاه شدن)
Blackening+Oiling یک پوشش محبوب برای اتصال دهنده های صنعتی است زیرا ارزان ترین است و قبل از مصرف سوخت ظاهر خوبی دارد.به دلیل سیاه شدن تقریباً قابلیت جلوگیری از زنگ زدگی ندارد بنابراین بدون روغن به سرعت زنگ می زند.حتی در صورت وجود روغن، آزمایش نمک پاشی فقط می تواند 3-5 ساعت طول بکشد.
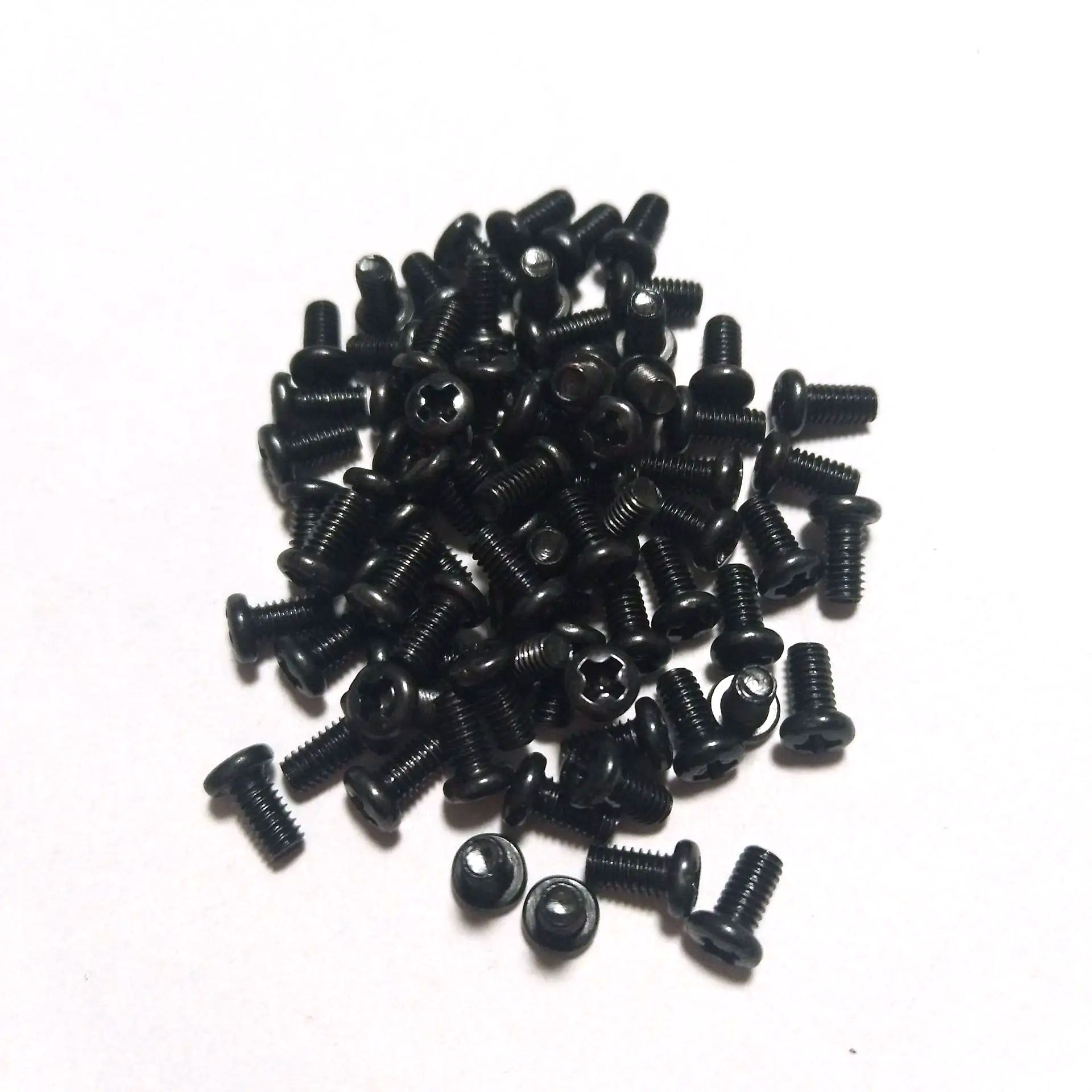
4. پارتیشن آبکاری
آبکاری کادمیوم در مقایسه با سایر عملیاتهای سطحی مقاومت بسیار خوبی در برابر خوردگی، به ویژه در محیطهای جوی دریایی دارد.هزینه تصفیه مایع زباله در فرآیند آبکاری کادمیوم بالا است و قیمت آن حدود 15 تا 20 برابر آبکاری روی است.بنابراین در صنایع عمومی فقط برای محیط های خاص استفاده نمی شود.بست های مورد استفاده برای سکوهای حفاری نفت و هواپیماهای HNA.
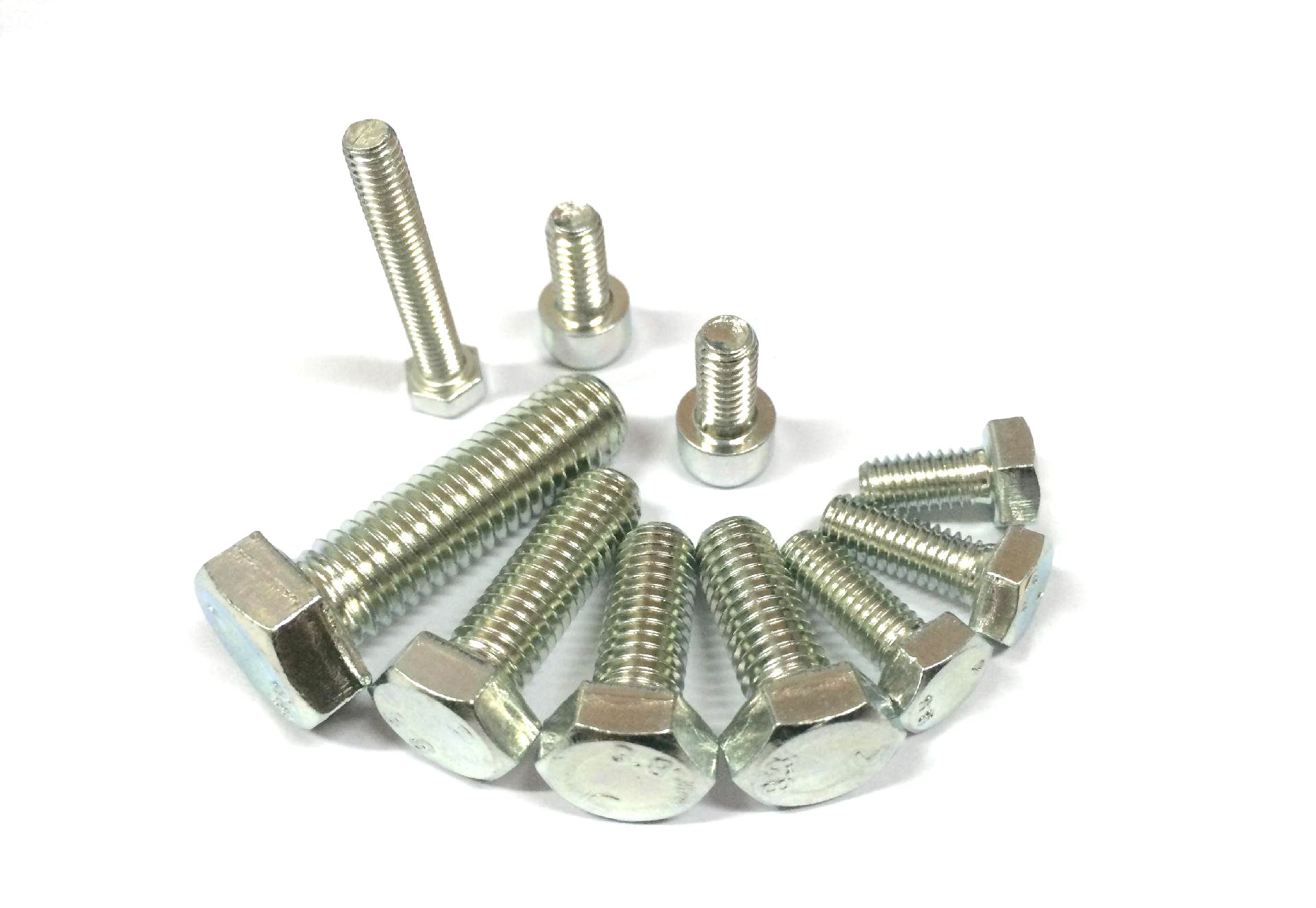
5. آبکاری کروم
روکش کروم در جو بسیار پایدار است، به راحتی تغییر رنگ نمی دهد و درخشندگی را از دست نمی دهد و دارای سختی بالا و مقاومت در برابر سایش است.استفاده از روکش کروم روی اتصال دهنده ها معمولاً برای اهداف تزئینی استفاده می شود.به ندرت در زمینه های صنعتی با الزامات مقاومت در برابر خوردگی بالا استفاده می شود، زیرا اتصال دهنده های کروم اندود خوب به اندازه فولاد ضد زنگ گران هستند.فقط زمانی که استحکام فولاد ضد زنگ کافی نباشد، به جای آن از بست های کروم اندود استفاده می شود.
برای جلوگیری از خوردگی، ابتدا مس و نیکل باید قبل از روکش کروم آبکاری شوند.روکش کروم می تواند دمای بالای 1200 درجه فارنهایت (650 ℃) را تحمل کند.اما مشکل تردی هیدروژنی نیز مشابه الکتروگالوانیزه کردن وجود دارد.
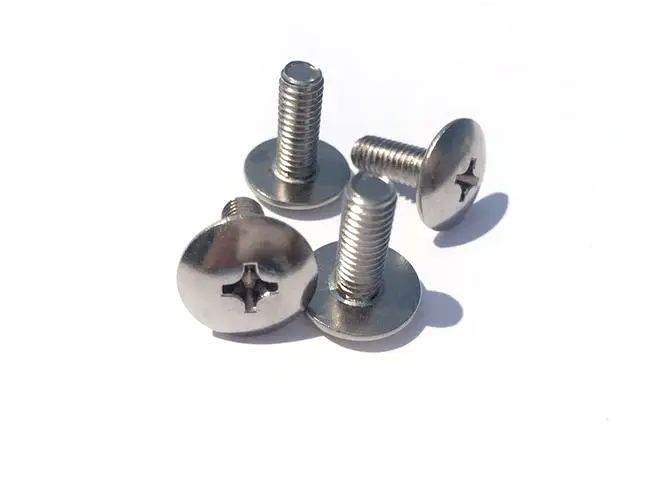
6. آبکاری نیکل
عمدتاً در مناطقی استفاده می شود که به ضد خوردگی و رسانایی خوب نیاز دارند.به عنوان مثال، پایانه های خروجی باتری های خودرو.
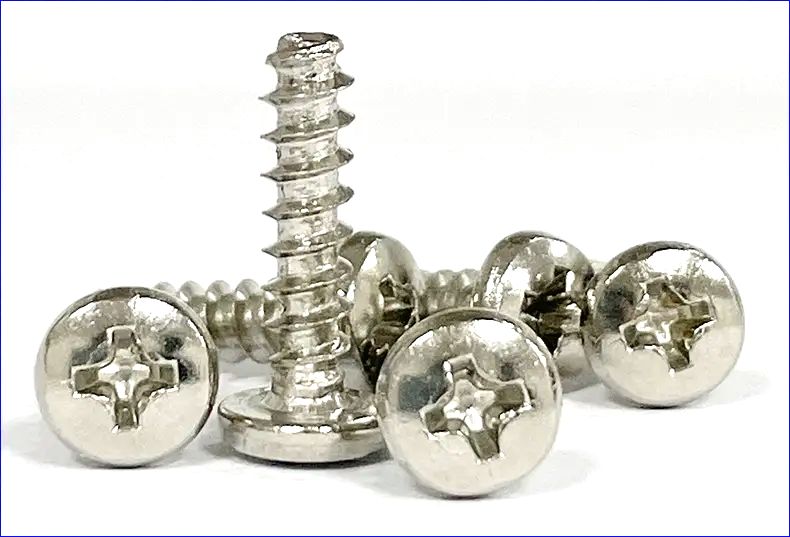
7. گالوانیزه گرم
گالوانیزه گرم یک پوشش انتشار حرارتی از روی است که به مایع تبدیل می شود.ضخامت پوشش بین 15 تا 100 میکرومتر است.و کنترل آن آسان نیست، اما مقاومت در برابر خوردگی خوبی دارد و اغلب در مهندسی استفاده می شود.در طی فرآیند گالوانیزه گرم، آلودگی شدیدی از جمله ضایعات روی و بخار روی وجود دارد.
به دلیل پوشش ضخیم باعث ایجاد مشکل در پیچ شدن رزوه های داخلی و خارجی در بست ها شده است.به دلیل دمای پردازش گالوانیزه گرم، نمی توان از آن برای اتصال دهنده های بالاتر از درجه 10.9 (340 ~ 500 ℃) استفاده کرد.
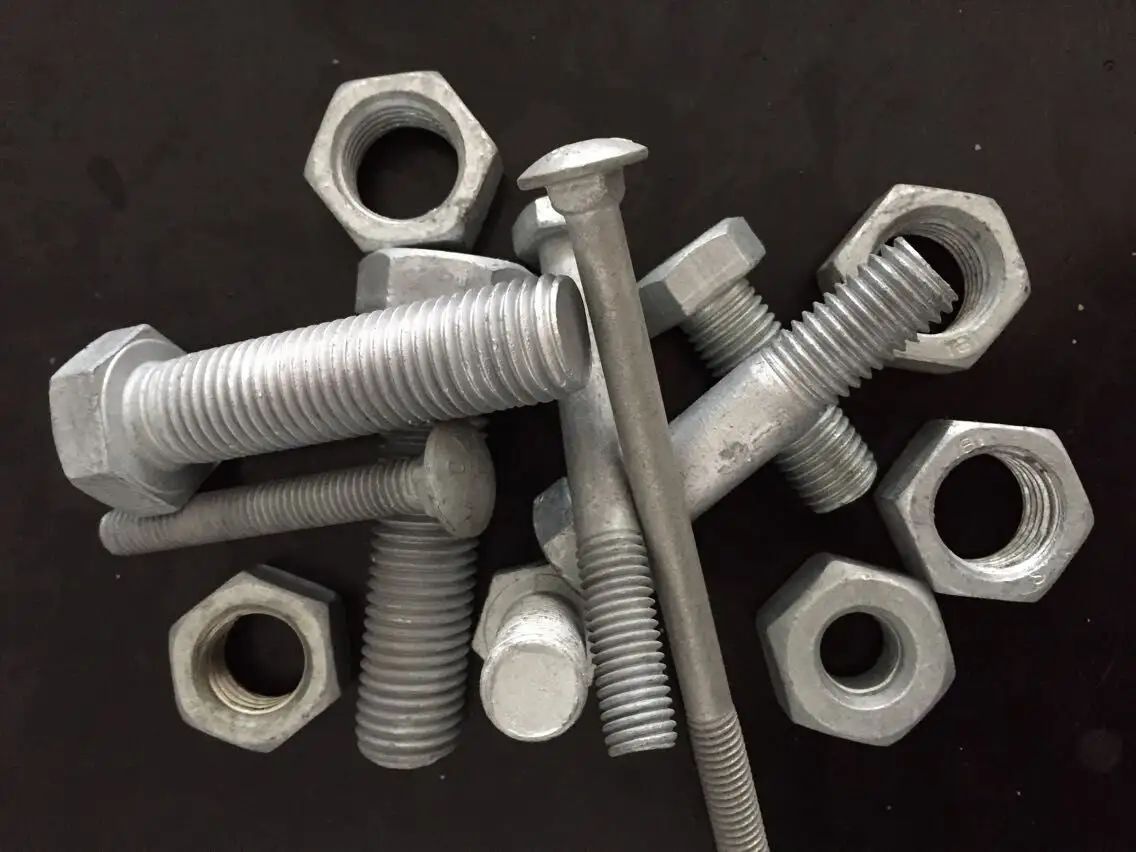
8. نفوذ روی
نفوذ روی یک پوشش متالورژیکی جامد انتشار حرارتی پودر روی است.یکنواختی آن خوب است و یک لایه یکنواخت هم در رزوه ها و هم در سوراخ های کور به دست می آید.ضخامت آبکاری 10-110 میکرومتر است.و خطا را می توان در 10٪ کنترل کرد.استحکام اتصال و عملکرد ضد خوردگی آن با زیرلایه در پوششهای روی (مانند الکتروگالوانیزه، گالوانیزه گرم و داکرومت) بهترین است.فرآیند پردازش آن بدون آلودگی و سازگار با محیط زیست است.
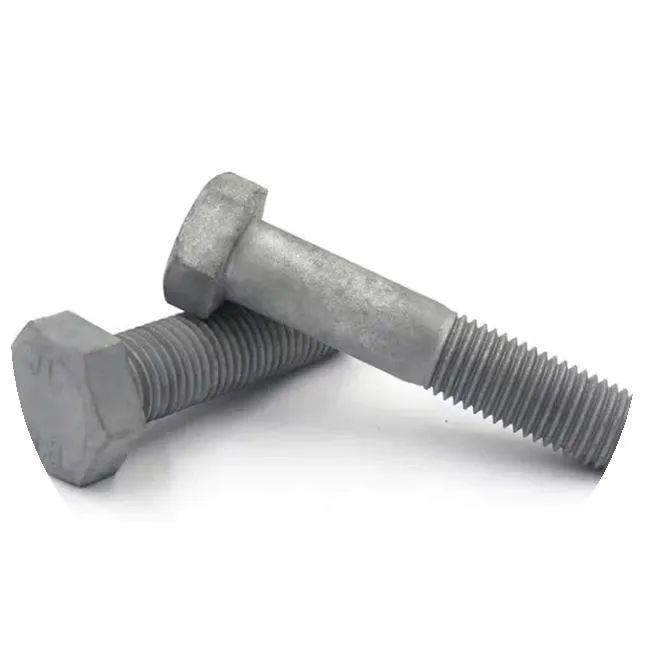
9. داکرومت
مشکل شکنندگی هیدروژن وجود ندارد و عملکرد قوام پیش بار گشتاور بسیار خوب است.بدون در نظر گرفتن کروم و مسائل زیست محیطی، داکرومت در واقع مناسب ترین برای اتصال دهنده های با استحکام بالا با نیازهای ضد خوردگی بالا است.
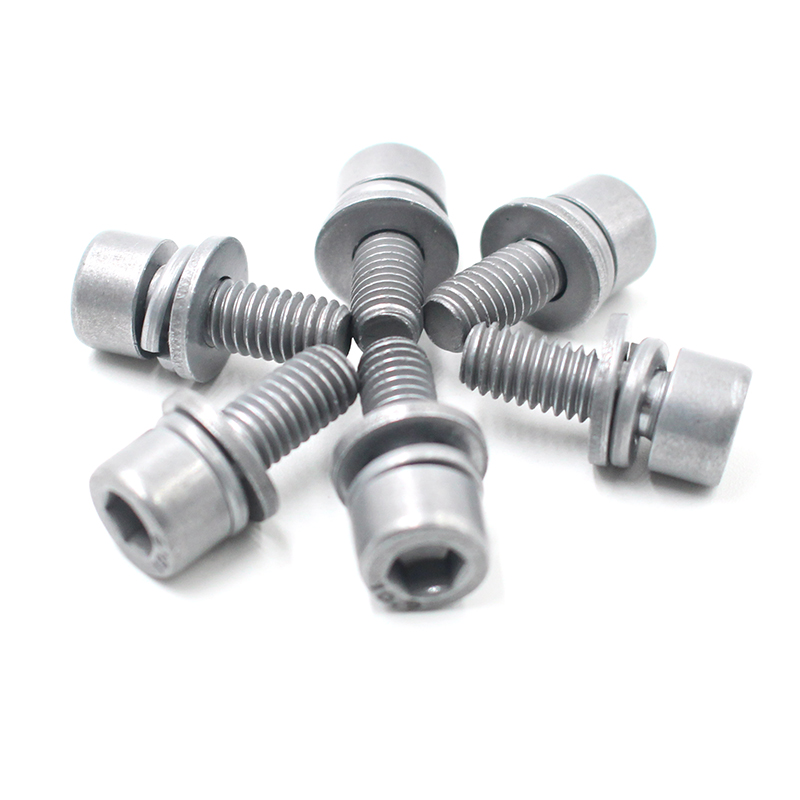
زمان ارسال: مه-19-2023